|
|
How do you swage bullets?
Bullet swaging is a method of using pressure to form a bullet, which is the inert metal portion of the cartridge
(which becomes a projectile when fired) by using pressure to flow the materials at room temperature.
Unlike casting, no heat or molten metal is used. The high pressure is applied with a special, powerful
press
(either hand or hydraulic powered) designed to hold a precision, diamond-lapped
die
(the vessel that holds the pressure and controls the bullet diameter) and both an internal (inside the ram) punch
and an external (in the press head) punch.
The punches press against the material inside the die from both ends, and cause it to flow, filling the die
and taking on the exact shape and finish of the die and punch ends. Safety, speed, precision, versatility, and
low cost for the number of weights are some of the benefits of swaging.
|
Click the picture of the bullet closest to what you want to make:
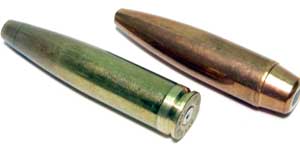 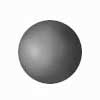 If you would like to see specific swaging operations, terminology, advantages, bullet designs, standard bullet specs and what equipment you need to start, jump to the pages linked to these underlined words. If you would like to know more about swaging and how it is done in general terms, read on...
Swaging Video
|
These are the basic variations in bullets that require different sets or combinations of the swage dies:
-
LSWC
-
(lead, swc-nose style, any base including GC and BG) Uses LSWC-1 swage die. Bullet nose and base are formed against punch
ends.
-
OGIVAL LEAD
-
(smooth curve nose to shank, all lead, any base) Uses a
CSW-1
core swage for exact weight, and a
PF-1
point form die for bullet shape and size. Ogive is formed against the interior die wall, so there is no "nose punch".
There is an ejection pin instead.
-
JSWC
-
(jacketed shank, swc-nose style, any base) Uses the JSWC-2 die set, which consists of the
CSW-1
core swage and the
CS-1
core seat die, to swage an exact weight core and then assemble it into a jacket while forming the base and nose
against punch ends.
-
FJFB
-
(full jacket, flat base open tip, any ogive shape) Uses the FJFB-3 die set, which consists of the
CSW-1
core swage, the
CS-1
core seater, and the
PF-1
point former. The core is swaged to weight in the
CSW-1
core swage, then placed inside a jacket. The jacket and core are expanded and any hollow cavity or cup base shape
applied during core seating in the
CS-1
die. The ogive or nose curve is formed in the
PF-1
point forming die.
-
LTFB
-
(full jacket, flat base lead tip, any ogive shape) Uses the LTFB-4 die set, which consists of the FJFB-3 plus a
LT-1
lead tip finishing die. The bullet is made exactly like the previous item, except that enough lead is put into the
jacket so it protrudes from the tip. The
LT-1
lead tip die is used to clean up and reshape this extra lead so it forms a perfect lead tip against a punch in the
LT-1
die. (The same
LT-1
die can be used for many different shapes in the same caliber, by using different internal punches).
-
RBTO
-
(full jacket, rebated boattail, open tip,any ogive shape) Uses the RBTO-4 Rebated Boattail, Open tip die set which
consists of a
CSW-1
core swage to adjust core weight, a BT-1 boattail preforming die which substitutes for the core seater and starts the
angled base on the jacket as the core is pressed into the jacket, a BT-2 boattail finishing die which finishes the base
with a sharp rebate, and a
PF-1
die with a base punch that matches the rebated boattail angle and depth.
-
RBTL
-
(full jacket, rebated boattail, lead tip, any ogive shape) Uses the RBTL-5 die set, which is just the RBTO-4
described above plus the
LT-1
die to finish the lead tip, exactly as with a flat base lead tip bullet.Note that there is also a FRBL-6 die set,
which merely adds the flat base capability so you can make both RBT and FB bullets, open or lead tip.
Briefly, here are the steps in making a lead tip, flat base rifle bullet:
-
1. Cut the core
-
Use Corbin LW-10 lead wire and PCS-1 core cutter, ...or...cast the core with the Corbin CM-4 core mould and your scrap
lead
-
2. Swage the core
- Use
CSW-1 core swage to get exact weight. Just put the core into the die, and adjust the external
punch holder so the press always goes to the top of the stroke so you leave a consistent volume in the die.
Equal volume equals equal weight left: the rest of the lead bleeds out three holes in the side of the die.
-
3. Seat the core
-
Put core in jacket, press together in
CS-1
core swage. Use a little CSL-2 Corbin Swage Lube on your fingers, and give the jacket a slight roll to spread the
lube on it as you drop it into the die. Just press gently, to make sure the jacket expands.
-
4. Form the point
-
Shape the ogive in the
PF-1
point form die. Depending on how much lead you used for a given length of jacket, you can have an open tip or a
lead tip at this point. The open tip is finished.
-
5. Finish the tip
-
For sharper lead tips, reshape in
LT-1
lead tip die. This die has a punch that is the right shape to match the point form ogive curve, and just gently
finishes the lead tip to perfection.
And here are the steps to make a paper patched rifle bullet, or a hollow base wadcutter pistol bullet, or any similar
all-lead bullet regardless of the nose and base shape:
-
1. Cut the core
-
Use Corbin LW-10 lead wire and
PCS-1
core cutter ...or...cast the core with the Corbin CM-4 core mould and your scrap lead
-
2. Swage the bullet
-
Use LSWC-1 lead swage die with desired nose and base punch, to form any lead bullet with a small shoulder
(punch edge forms this...eliminating it means using a point form die instead).
Obviously, there are thousands upon thousands of other variations of bullets you can swage, but all of them simply add a
hollow point punch or a boattail base, or serrate the jacket, or put teeth on the end of the bullet by pushing it
against a special punch...it's not brain surgery!
Once you know how to make a couple of basic styles, you know enough to make almost any bullet. Some special shapes
may take a special tool, such as the perfect round ball. But by and large, the instructions that come with
the dies are more than sufficient to teach a person who is capable of making handloads how to swage bullets.
Sometimes the sheer size of our web site and the wealth of tools we offer scares off people who don't take the
time to look closer, and see that any given bullet only uses a tiny bit of all this equipment.
We make nearly everything that has been made, for swaging, because we've been dedicated to developing the
technology for over 30 years. But you don't need ALL of it! You don't even need very much of it...just the
items that make the bullets you are most interested in building.
By taking the time to look over the design, terminology, and swaging instructions step by step, you'll soon come
to realize that it is very basic, simple technology: you just press metal into shape within dies,
expanding the diameter as you shorten the length slightly in each step. What makes it unusual,
and the reason fewer people swage than cast bullets, is the high precision required to build the swage dies
that can handle enough pressure to actually expand and shape solid, room-temperature metal. Making the
dies isn't that easy. But using them is easier than reloading.
Because you are in total control over the materials and technique used to make your own bullets, you have
an opportunity to build far better bullets for your own purpose than the mass producers will ever have.
They must make millions of the same bullet to sell to tens of thousands of average shooters...so naturally,
they can't be blamed for building an average product. It must be that way, by definition of mass marketing.
You, on the other hand, are one person, and if you have read this far, you are not an average shooter.
You may benefit by using an above average bullet, made the way you want it, in the exact weight, shape,
style, and construction you've always wanted for a given purpose but couldn't buy from a high volume mass
production supplier. They can't afford to make you a box of bullets, just the way you want them. But you
can do it easily.
|
Swaging is faster, easier and more safe than the alternative of casting, since no hot lead is used.
You can instantly make a finished bullet by putting material inside the die and squeezing it.
It pops out on the ejection stroke, finished to far higher precision than is possible with constantly
changing temperatures of hot metal with their expanding and cooling moulds. A swage die operates constantly at
room temperature, so it remains the same diameter and is not influenced by temperature changes to the
degree that you find in cast bullets. Because you don't have to wait for lead to melt, make a lot of
test casts to heat the mould, and then clean up the mess afterward, swaging is faster than casting.
The precision of swaged bullets is legendary. Every world class record except perhaps in cast bullet competitions where
swaged bullets are not permitted has been won by someone shooting a swaged bullet. Every mass producer and custom
bullet maker involved in jacketed bullets or high precision lead bullets uses swaging equipment, most of it from the
Corbin
die-works
in White City, Oregon.
Olympic target shooters, military sniper teams, elite special forces groups, law enforcement and security
organizations charged with protecting lives and property, and major defense contractors all use Corbin swaging
presses, dies, and tools in their prototype development and short run production
(we do not build mass production equipment). Everything about our approach to the business aspect of bullet
making is aimed toward a secure, comfortable business you can run from your home with one or two people.
The concept of exotic, specialty bullets sold at high return to a limited but intensely loyal clientelle through a
low overhead direct-mail operation can make more net profit than a mass production company making millions of bullets
but only pennies on each bullet.
|
Bullet swaging is extremely simple to do, but because for 30 years Corbin has been developing every imaginable
kind of bullet and the tools to build them, we've built up a formidable arsenal of equipment to make any kind of
bullet from a round musket ball to a sophistocated multi-section tungsten powder core rebated boattail.
Each step is easy, but different kinds of bullets usually require slightly different procedures and possibly
different kinds of dies. A simple semi-wadcutter or lead bullet can usually be made in one single stroke, in a
LSWC-1-
type die. You can also make the bullet jacket yourself, from strip or from tubing, and then use it to make a
jacketed bullet. This may take from four to eight dies, depending on the shape and style. Or you can purchase
ready-made bullet jackets from us. We have everything from the
lead
wire to core moulds for using your own scrap lead, from ready made
jackets
to raw materials like coils of copper strip and/or lengths of cut tubing, and exotic bullet materials like
powdered
tungsten,
powdered brass and copper, plastics and other materials.
Chemical
products such as swaging lube and liquid jacket, bore cleaners and laps, and core bond flux can be ordered from
Corbin as well.
|
To get a really good understanding of swaging only takes a few minutes experimenting with the dies.
But you can also adsorb years of hard-learned knowledge in a few hours by reading the Corbin Handbook of Bullet
Swaging, or get the full 30 years of experiments and developments with
bullet designs
in our multi-media swaging
pack books, ebooks, and video
dedicated to the art and science of bullets you can make at home with relatively simple equipment.
|
Equipment can run from a simple
die
that works in your reloading press and makes an infinite number of weights in a single diameter to a roller
bearing steel press and 3-die jacketed bullet outfit that can make solids, soft points, open tips, hollow points,
and many other styles with a flat base design. Boattail systems cost slightly more, since there are additional dies
involved. Certain kinds of bullets require larger presses (such as the bullets which are made of solid copper or use
hard lead alloys).
Commercial
business packages usually generate from 200 to 500 percent return on investment each year after the start-up period.
A swaging die or set of dies can make a wide range of bullet weights and styles. A casting mould makes one basic
weight and style only, and you buy another mould for each change. Not so with swaging. It has been said that a
single swage die is equivalent to about 500 moulds, in regard to all the bullet weights and styles it can make.
Most people are able to make far better bullets than they have ever purchased, in unlimited weights and styles:
it is like having a rich Uncle working at a military R&D lab with unlimited access to the machinery, except you don't have
to worry about getting caught!
|
As to bullet cost, if you make the same style as you cast now, it costs no more. Whatever your lead costs is what the
bullet costs. If you make a jacketed bullet, you have the jacket material cost to add, of course. Most ready-made
benchrest quality jackets are about eight cents. You can make tubing or drawn strip jackets at anywhere from three to
thirty cents each, depending on the caliber and thickness, where you get the material and so forth.
Scrap materials can be free or nearly so. Top grade materials in thick, long, large calibers like the 50 BMG push the
upper limit of this range. But the bullets you make are the same or better quality as the ones selling every day
for an average of $1.50 each!
Some bullets can be made nearly free of cost:
fired .22 cases make excellent
jackets
for .224 and .243 bullets, and acceptable ones for .257 and .251 bullets. Scrap
lead
can be cast into bullet cores using a four cavity
Corbin mould.
It doesn't cost thousands to get the dies and make good bullets! Many people have that impression, and it isn't
true. We do make tooling that costs in that range but that is very special, semi-automated or automated
tooling for
high powered presses that we build, for custom bullet businesses. You don't have to buy that to make bullets or
jackets: we have lower volume production equipment for far less cost. It is slower, but just as precise. The
cost per finished jacketed bullet is typically about six to eleven cents, or about half the cost of the much
lower quality commercial bullets produced for mass consumption and marketing "over the counter".
|
No mass produced bullet can ever be as well built as the custom, exotic designs that are produced by small custom
shops for big game, simply because there are not that many people who would understand, appreciate, and pay for such
bullets. The average shooter controls the mass market. He is the one to whom everything must appeal in the mass
production line-up. Not you. If you were the average shooter, you wouldn't even be reading this!
Tell me you haven't at some point said to yourself, "I wish there was a bullet made like this..." and then just
shrugged because you knew there wasn't. Well, with swaging dies, you can make it yourself. And if it works as you
feel it should, you can probably sell some to other above average shooters who have also wanted something like that
and couldn't get it before.
Swaging is the power to let your imagination grow, and see the results immediately. In a few minutes times, you
can make a dozen different kinds of bullets with the same equipment, just by changing the technique you use, what
you put into the bullet, how you insert the components, what components you decide to use.
|
Answers to commonly asked questions about swaging.
|
Technical support and sales e-mail:
sales@corbins.com
FAX: 541-826-8669 -
- PHONE: 541-826-5211
|
CORBIN
PO Box 2659, White City, OR 97503 USA
|